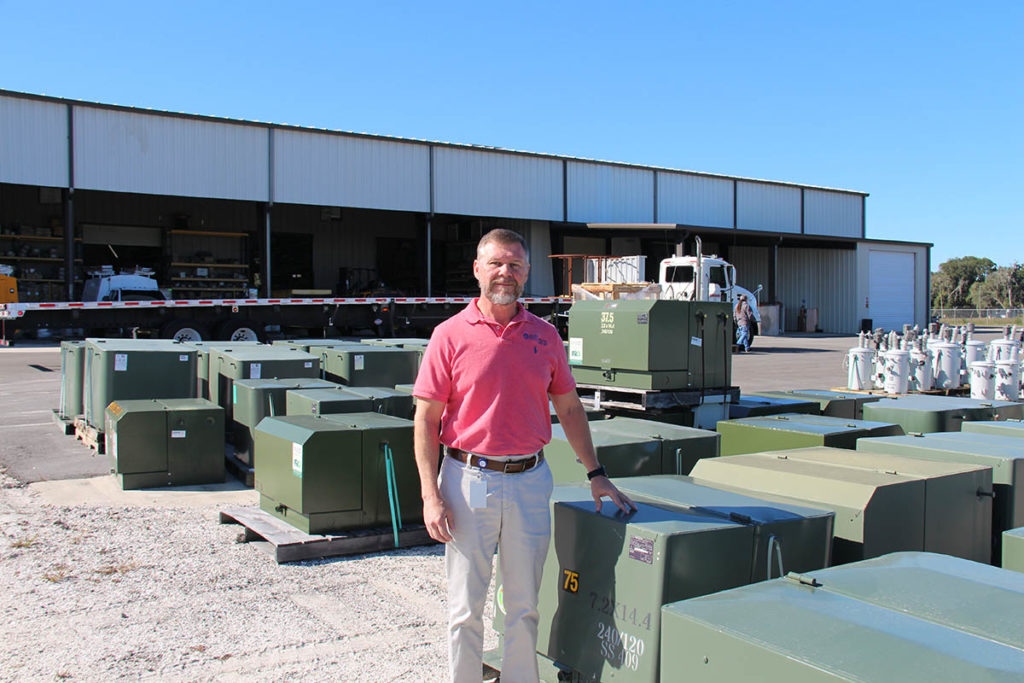
As electric cooperatives contend with global supply chain disruptions caused by the COVID-19 pandemic, they’re working with their suppliers, vendors and logistics providers to meet demand for parts and other key components essential to keeping power flowing.
“We’re facing long lead times for pad-mounted transformers and PVC pipe used for conduits for underground distribution,” said Tim Gibson, purchasing agent for Wauchula, Florida-based Peace River Electric Cooperative. “Digital meter availability has also been a big problem due to the worldwide shortage of microchips, so we’ve projected six-month demand and ordered them for staggered delivery to meet our needs.”
Long lead times for some parts, like polyvinyl chloride pipe and fittings, have been extended due to feed stock shortages or curtailed operations at petrochemical plants in Texas and Louisiana caused by weather or staffing challenges. Pandemic-related concerns and shipping delays have also prompted some warehouse managers to increase reserves on hand by doubling and even tripling up on their inventories.
“We’re routinely looking at the usage history of our customers so we can anticipate their actual demand for 2022 and the following year,” said Bret Curry, sales manager at Arkansas Electric Cooperatives Inc. The Little Rock-based logistics and service arm of the Arkansas statewide association serves as the principal parts and equipment supplier for about 400 utilities, including co-ops in five Mid-South states.
AECI also regularly consults with members of the Electric Utility Distribution Association, which includes nine member-owned logistics suppliers serving member-owned and public power interests. Several members of EUDA are reporting similar concerns across their client bases.
“Long lead times have caused inventory levels to fluctuate greatly—making it very hard to manage stockouts,” said Johnny Andrews, chief operating officer of Texas Electric Cooperatives’ manufacturing and distribution services division.
Among the strategies TEC has employed to address the supply shortage has been meeting demand with reconditioned equipment, like meters and transformers.
“This approach has worked extremely well for TEC due to the support of companies like Emerald Transformer and Allegiant Utility Services, which manufacturers and refurbishes meters,” said Andrews. “Both of these organizations have stock of refurbished equipment, offer product warranties that are similar or better than the original equipment manufacturers and can also refurbish and repair the co-ops’ equipment as well.”
While several EUDA members are advising clients that logistics challenges could linger well into 2023, the end of the 2021 Atlantic hurricane season may provide a bit of relief. Storm activity along the Gulf and Atlantic coasts has been less damaging than normal this year, and seasonal reserves of parts and equipment built up since the spring will begin flowing back into inventories in December.
Still, co-ops are being encouraged to work with local developers on major projects to divide larger jobs into several phases, allowing for delivery of essential parts and components over extended periods.
“The key is planning, particularly for large developments or subdivisions slated for construction over the next three to four years,” said AECI’s Curry. “Talk to your builders and developers and tell them just what we’re telling our distribution co-ops. If they tell you they need to build out infrastructure for 100 new homes tomorrow, that’s not likely to be possible in this environment, and there are no hard expectations of that improving anytime soon.”
Derrill Holly is a staff writer for NRECA.